Gestione del magazzino e diverse modalità di picking
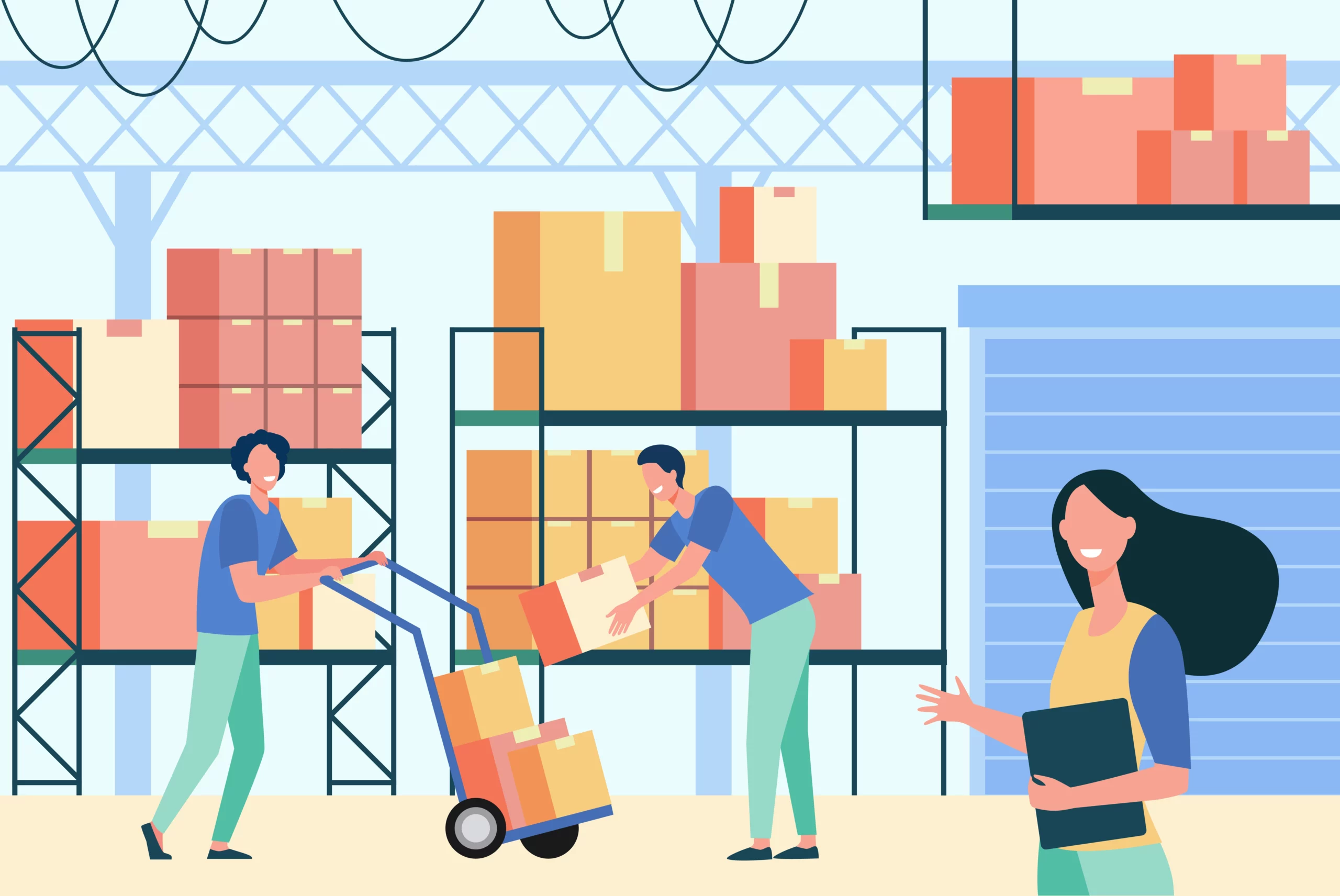
Tempo di lettura: 4 minuti
Che cos’è il picking di magazzino?
La gestione del magazzino rappresenta una componente fondamentale nell’evasione degli ordini. Tra le varie operazioni che ne garantiscono l’efficienza, il picking, ovvero la raccolta degli articoli necessari per completare un ordine, riveste un ruolo centrale.
Il picking consiste nel prelevare e raccogliere dalle diverse aree e scaffali del magazzino i prodotti richiesti da uno o più ordini per prepararli alla spedizione. Questo processo può essere eseguito manualmente o con l’ausilio di tecnologie automatizzate.
Poiché le diverse modalità di prelievo in magazzino hanno un impatto diretto sulla soddisfazione del cliente, sulla reputazione aziendale e sulla redditività, migliorare questa attività è una priorità assoluta per le aziende.
In questo articolo andremo ad esaminare le principali modalità di picking, illustrandone le caratteristiche e l’applicazione in contesti specifici.
Order picking
L’order picking, noto anche come picking per ordine, è il metodo più tradizionale e semplice, in cui un operatore preleva tutti gli articoli necessari per completare un singolo ordine prima di passare al successivo. Questo può essere eseguito manualmente (picking manuale “carta e penna”) o con dispositivi mobili per la scansione dei codici a barre.
Questo metodo è adatto a magazzini di piccole dimensioni o con un volume di ordini relativamente basso. Ciononostante, la sua semplicità operativa lo rende ideale anche per le aziende con ordini che variano notevolmente in dimensioni e complessità.
In un magazzino che utilizza l’order picking, ogni operatore è responsabile del completamento di un ordine specifico. Questo approccio minimizza il rischio di errori poiché l’attenzione dell’utente è focalizzata su un solo ordine alla volta. Tuttavia, come visto in precedenza, può risultare inefficiente in magazzini di grandi dimensioni o con un alto volume di ordini, poiché gli operatori potrebbero dover percorrere lunghe distanze per prelevare gli articoli necessari, aumentando così i tempi complessivi di prelievo.
Vuoi saperne di più?
Pick & Pack
Il pick&pack è un processo in cui gli articoli vengono prelevati e contestualmente imballati per la spedizione. Questo metodo funziona bene per l’e-commerce B2C (Business to Consumer), dove la velocità di evasione degli ordini è fondamentale. Gli operatori prelevano gli articoli richiesti e li imballano direttamente, preparando l’ordine per la spedizione in un’unica operazione. Questo approccio riduce i tempi di elaborazione, consentendo una rapida risposta alle esigenze dei clienti finali.
Batch picking
Il batch picking, o picking a lotti, è una modalità in cui un operatore preleva articoli per più ordini contemporaneamente. Gli ordini vengono raggruppati in batch, e gli articoli comuni a più ordini vengono prelevati insieme. Questa modalità risponde alle esigenze di magazzini con un alto volume di ordini e con molti articoli comuni.
Il prelievo in batch è più efficace quando gli operatori devono percorrere lunghe distanze nel magazzino per evadere più ordini con lo stesso SKU (Stock Keeping Unit).
Un esempio pratico può essere osservato in un magazzino che gestisce la distribuzione di prodotti elettronici. Supponiamo che più ordini richiedano batterie standard. Con il batch picking, l’operatore preleverà tutte le batterie necessarie per quegli ordini in una sola volta, riducendo i tempi di percorrenza.
Il batch picking richiede un sistema di gestione degli ordini sofisticato per coordinare i lotti e assicurarsi che gli articoli vengano correttamente separati per ciascun ordine, prevenendo gli errori.
Zone picking
Il zone picking prevede la suddivisione del magazzino in diverse zone, ciascuna gestita da operatori specifici che, per ogni ordine cliente, sono responsabili del prelievo dei soli articoli stoccati all’interno della propria zona. L’ordine, in totale, viene poi assemblato centralmente dopo che tutti gli articoli sono stati prelevati dalle diverse zone.
Questo metodo è efficace in magazzini di grandi dimensioni o con una vasta gamma di prodotti. Ad esempio, in un magazzino di abbigliamento, una zona potrebbe essere dedicata ai capi invernali, un’altra agli accessori, e così via. Gli operatori diventano esperti nella loro zona, il che può ridurre gli errori e aumentare la velocità di picking.
In questo caso, è necessario un sistema ben coordinato per assemblare gli ordini finali, poiché eventuali ritardi in una zona possono influenzare l’intero processo.
Wave picking
Il wave picking combina elementi del batch picking e del zone picking. Gli ordini vengono suddivisi in “onde” e prelevati in sequenze temporali specifiche. Ogni onda rappresenta un gruppo di ordini che devono essere completati insieme, ottimizzando il flusso di lavoro in tutto il magazzino.
In un grande centro di distribuzione, il wave picking può essere utilizzato per sincronizzare le operazioni di picking con altre attività, come il ricevimento delle merci e la spedizione.
Per esempio, durante una particolare onda, gli operatori preleveranno articoli per gli ordini che devono essere spediti entro la stessa finestra temporale. Questo metodo permette una gestione più fluida e coordinata delle operazioni di magazzino, migliorando l’efficienza complessiva.
Picking Multi Cliente e Multi Ordine
Il picking multi-cliente/multi-ordine è una modalità in cui gli operatori prelevano articoli destinati a diversi clienti o ordini in un’unica operazione. Questo metodo è utilizzato per le spedizioni miste in Italia, dove più ordini di diversi clienti vengono raccolti insieme per ottimizzare l’efficienza, specialmente in contesti con un alto volume di ordini (es. ordini e-commerce). Gli articoli sono poi separati e imballati in base a ciascun cliente o ordine specifico.
Se nessuna di queste strategie si adatta al processo logistico aziendale, è possibile combinare tra loro diverse modalità di picking, attraverso un’analisi accurata e l’implementazione di un moderno sistema di gestione magazzino (WMS – Warehouse Management System).
Processi di picking automatizzati
Per ottimizzare le attività di picking e i processi di magazzino nell’insieme, possono essere impiegate tecnologie robotiche e semi-robotiche. Le soluzioni di picking automatizzato variano ampiamente, ma le più efficaci sono quelle che si integrano senza soluzione di continuità nei processi esistenti, collaborando con i team di lavoro.
Pick-to-Light
Il sistema Pick-to-Light utilizza scanner di codici a barre e LED installati sugli scaffali del magazzino. Gli operatori iniziano scansionando il codice a barre sulla scatola di spedizione. Successivamente, i LED corrispondenti agli articoli necessari si illuminano, guidando l’operatore nella raccolta degli articoli. Questo sistema riduce i tempi di picking e i costi associati al lavoro, migliorando la velocità e la precisione dell’evasione degli ordini.
L’integrazione del WMS con il Pick to light a scaffale o a carrello con “led-light” è particolarmente strategica per le evasioni multiordine e/o multicliente poiché aumenta la velocità di prelievo e riduce gli errori.
Voice Picking
Il Voice Picking è una tecnologia hand-free che guida gli operatori del magazzino attraverso indicazioni vocali. Gli addetti, dotati di apposite cuffie, ricevano istruzioni vocali su quali SKU prelevare e dove trovarli, liberando le mani e gli occhi da altre attività. Questo metodo migliora la produttività, consentendo ai lavoratori di concentrarsi sul picking senza distrazioni.
Mobile Scanner Picking
Il Mobile Scanner Picking utilizza dispositivi portatili come smartphone o scanner per confermare e monitorare gli ordini in tempo reale. Attraverso il software WMS, i magazzinieri possono scansionare i codici a barre degli articoli e aggiornare immediatamente lo stato degli ordini. Man mano che gli articoli vengono prelevati, vengono scansionati, garantendo l’aggiornamento in tempo reale delle giacenze.
Robot Mobili Collaborativi
Questi robot assistono gli operatori umani, gestendo il compito manuale di spostare i prodotti. Possono essere programmati per seguire vari metodi di picking in magazzino, ottimizzando i percorsi in tempo reale utilizzando l’intelligenza artificiale.
Vuoi saperne di più?
Fattori che condizionano la scelta di un sistema di picking
La modalità di picking utilizzata nel sito logistico può avere un impatto significativo sull’operatività e sulla sicurezza del magazzino. È fondamentale considerare vari fattori:
- caratteristiche dei prodotti (Tipo e Dimensione)
- numero totale di ordini
- numero di righe per ordine
- articoli comuni a più ordini
- numero prese per ordine
- quantità per presa
- numero totale di referenze
- tipologia di picking
- frazionato per Prezzi o Confezioni
- UDC intere
- orari di lavoro degli addetti al picking
- sicurezza dei lavoratori
- numero di lavoratori disponibili
- frequenza degli ordini
Una delle massime priorità aziendali dovrebbe essere la creazione di obiettivi in cui gli operatori di magazzino siano incoraggiati a selezionare il maggior numero di ordini nel minor tempo possibile senza sacrificare la precisione o la sicurezza. Ciò può essere ottenuto progettando il magazzino in modo da facilitare una maggiore densità di prelievo.
Obiettivi chiave includono:
- Minimizzare il tempo di spostamento: ridurre il tempo trascorso a spostarsi tra articoli e ottimizzare i percorsi.
- Garantire un ambiente di lavoro sicuro: implementare misure di sicurezza ed ergonomiche per prevenire infortuni.
- Migliorare la precisione del picking: utilizzare tecnologie come voice picking e pick-to-light per ridurre gli errori.
- Massimizzare l’uso dello spazio: effettuare una mappatura di magazzino per riorganizzare e ottimizzare la disposizione degli articoli e facilitare il flusso del lavoro.
Con l’evoluzione della tecnologia, l’avvento dell’intelligenza artificiale e i sistemi di Warehouse Management System (WMS) moderni, le aziende dispongono di un enorme potenziale per una gestione impeccabile delle attività logistiche.
Considerazioni finali
Come visto in questo articolo, la scelta della modalità di picking e delle tecnologie di automazione dipende da vari fattori, tra cui le dimensioni del magazzino, il volume degli ordini, la varietà dei prodotti e le specifiche esigenze operative dell’azienda.
Questi strumenti avanzati non solo migliorano l’efficienza e la precisione delle operazioni logistiche, ma offrono anche nuove opportunità per ridurre i costi operativi e soddisfare meglio le esigenze dei clienti.
Vuoi rendere più strategica la tua logistica? Prenota una consulenza gratuita con un nostro analista e scopri STOCKFORCE WMS, il sistema di gestione magazzino integrabile al tuo ERP, altamente configurabile e con funzionalità specifiche per ogni settore.